Logistics Aspects of Serving B2B and B2C Customers
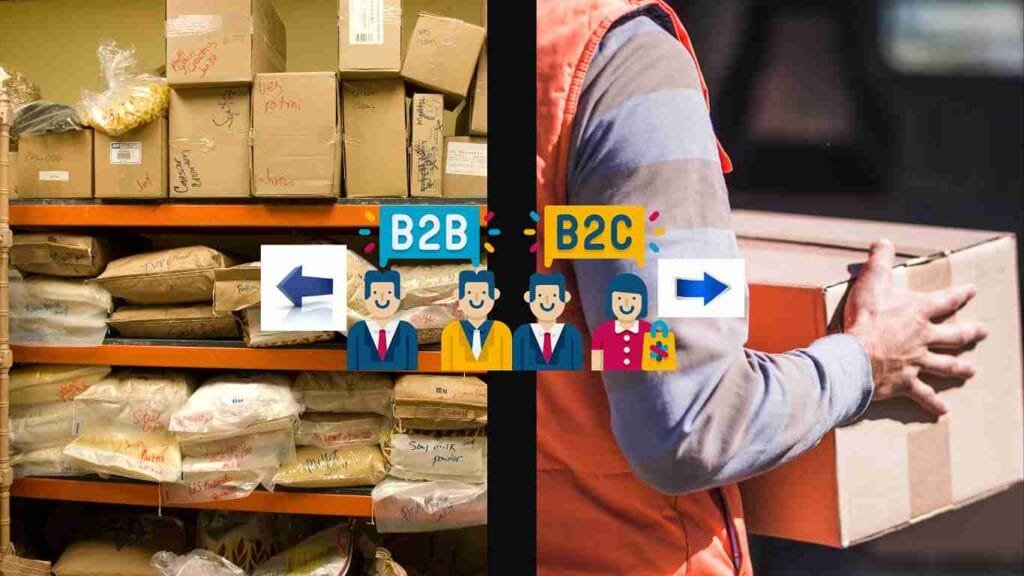
In today’s fast-paced global economy, logistics plays a critical role in meeting the ever-evolving demands of both B2B (Business-to-Business) and B2C (Business-to-Consumer) customers. Understanding the nuances of logistics for each model is essential for optimizing efficiency, reducing costs, and improving customer satisfaction. In this blog, we’ll explore the key logistics aspects involved in serving B2B and B2C customers, from inventory management systems to last-mile delivery services, and highlight sustainable logistics strategies that can enhance overall business operations. Understanding the Differences Between B2B and B2C Logistics Before diving into specific logistics solutions, it’s important to understand the primary distinctions between B2B and B2C logistics: Both B2B and B2C logistics require specialized strategies to ensure smooth and efficient operations, but the priorities and processes differ significantly. Key Logistics Aspects of Serving B2B Customers 1. B2B Logistics Solutions B2B logistics solutions are designed to streamline the supply chain and reduce the complexities involved in moving large quantities of goods from one business to another. These solutions often involve dedicated fleets, advanced route planning, and specialized handling for bulk shipments. Companies that specialize in B2B logistics must be able to handle international shipping, customs clearance, and regulatory compliance, especially when dealing with global supply chains. 2. Inventory Management Systems (IMS) Efficient inventory management is crucial in B2B logistics, where the scale of operations is typically much larger. A robust Inventory Management System (IMS) helps businesses keep track of their stock levels, optimize warehouse space, and ensure timely replenishment of goods. This is particularly important for manufacturers and wholesalers who deal with large volumes of goods that need to be delivered within specific time frames. 3. Supply Chain Management Services Effective supply chain management services are essential for B2B companies. These services help optimize the entire logistics process, from procurement to final delivery. By leveraging technologies such as AI and blockchain, companies can improve visibility across the supply chain, anticipate potential disruptions, and mitigate risks. B2B logistics often involves multiple stakeholders and partners, which makes robust supply chain management critical to ensure a seamless flow of goods. Key Logistics Aspects of Serving B2C Customers 1. Order Fulfillment for eCommerce For B2C businesses, order fulfillment for eCommerce is a critical component of the customer experience. Consumers expect fast and accurate order fulfillment, often with same-day or next-day delivery. To meet these demands, businesses must invest in efficient warehousing, picking, packing, and shipping processes. Companies can leverage third-party logistics (3PL) providers to handle fulfillment, allowing them to scale operations quickly and efficiently. 2. Last-Mile Delivery Services One of the biggest challenges in B2C logistics is last-mile delivery services. This is the final leg of the delivery journey from the distribution center to the consumer’s doorstep. Efficient last-mile delivery is crucial for ensuring timely and cost-effective delivery. With the rise of eCommerce, many businesses have turned to tech-driven solutions, such as route optimization software and delivery drones, to improve the efficiency of last-mile delivery. In fact, last-mile delivery services are one of the most searched logistics topics, with businesses continuously seeking new ways to optimize delivery times and reduce costs. 3. Returns Management Solutions Returns are an inevitable part of the B2C logistics process. A well-structured returns management solution helps companies handle returns swiftly and cost-effectively, which is crucial for maintaining customer satisfaction. A strong returns process not only involves reverse logistics but also integrates seamlessly with inventory management and order fulfillment systems to ensure that returned products can be restocked or resold quickly. Sustainable Logistics Strategies for B2B and B2C Businesses As businesses continue to scale, there is an increasing emphasis on sustainable logistics strategies that minimize environmental impact and reduce operational costs. Both B2B and B2C companies are adopting green logistics practices, such as: Sustainability is not just a buzzword; it’s a growing priority for both B2B and B2C companies aiming to meet consumer demand for environmentally responsible practices while improving their bottom line. Conclusion: Optimizing Logistics for Both B2B and B2C Success Logistics is the backbone of both B2B and B2C business models, but the approaches and strategies vary. B2B logistics focuses on large-scale operations, efficient supply chain management, and specialized solutions such as inventory management systems, while B2C logistics prioritizes fast, cost-effective order fulfillment, last-mile delivery services, and seamless returns management. By embracing the right logistics solutions, businesses can not only enhance operational efficiency but also improve customer satisfaction. Moreover, by incorporating sustainable logistics strategies, companies can future-proof their operations, contributing to both environmental sustainability and long-term profitability. To stay competitive in the dynamic logistics landscape, businesses must continuously evaluate their logistics strategies, invest in the latest technologies, and adapt to the changing needs of both B2B and B2C customers.
Logistics and Financial Management in Supply Chain: Key Strategies for Efficiency and Growth
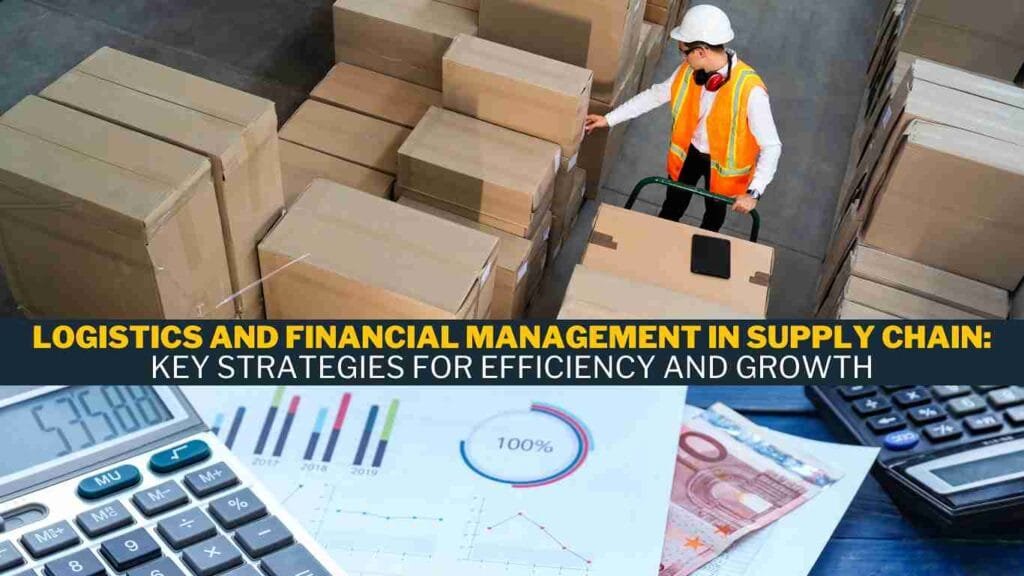
In today’s interconnected world, Supply Chain Management (SCM) has evolved beyond just a network of suppliers, manufacturers, and distributors. The integration of Logistics Management and Financial Planning in Supply Chainplays a pivotal role in ensuring not only operational efficiency but also financial success. In this blog, we’ll explore how effective logistics and financial management can streamline processes, optimize costs, and mitigate risks in the supply chain. Understanding Logistics Management in Supply Chain Logistics Management refers to the detailed planning, implementation, and control of the movement of goods and services across the supply chain. This includes transportation, warehousing, inventory management, order fulfillment, and more. Efficient logistics are crucial to meeting customer demand on time and at a competitive cost. The role of logistics within Supply Chain Management goes beyond just getting products from point A to point B. It’s about ensuring that products are delivered at the right time, in the right quantity, and at the right cost—optimizing resources and improving the customer experience. This is where effective Warehouse and Inventory Management becomes a game-changer. The Importance of Warehouse and Inventory Management Effective warehouse and inventory management is vital to ensuring that your logistics operations run smoothly. Having the right inventory at the right time prevents stockouts, reduces overstock situations, and helps maintain a smooth flow of goods. With modern technologies like Inventory Management Software and Warehouse Automation, businesses can keep track of inventory in real-time, optimize storage space, and enhance order fulfillment efficiency. However, poor inventory management can lead to issues like excess stock, dead stock, or delays in shipping—affecting overall cost optimization and customer satisfaction. Financial Planning in Supply Chain: A Key to Profitability Financial Planning in Supply Chain is critical for ensuring that resources are allocated efficiently, investments are made wisely, and financial risks are managed properly. An integrated approach to financial planning allows supply chain managers to foresee potential disruptions, identify cost-saving opportunities, and optimize cash flow. For instance, Supply Chain Finance Solutions—a set of financial instruments and tools designed to optimize cash flow and reduce working capital requirements—can offer businesses a way to accelerate payments and secure better credit terms from suppliers. These solutions can be especially useful for companies facing tight liquidity or in need of smoother financial operations across their supply chain. Supply Chain Finance Solutions: Empowering Financial Efficiency Supply Chain Finance Solutions can reduce payment cycles and allow for more flexibility in transactions between suppliers and buyers. By leveraging technologies like dynamic discounting or reverse factoring, businesses can improve working capital, enhance supplier relationships, and streamline financial processes throughout the supply chain. This not only lowers the financial burden but also improves the stability of the entire supply chain ecosystem. Risk Management in Logistics: Safeguarding Your Supply Chain Risk Management in Logistics is essential to protect your business from potential disruptions. In global supply chains, risks such as natural disasters, geopolitical events, and supply shortages are always present. If not properly managed, these risks can lead to significant delays, increased costs, and loss of customer trust. A comprehensive risk management strategy involves identifying potential risks, assessing their impact, and creating contingency plans. Whether it’s through sourcing from multiple suppliers or investing in technology to predict disruptions, having a proactive approach to risk management can safeguard your operations and prevent costly delays. Cost Optimization in Supply Chain: Driving Efficiency One of the primary goals of both Logistics Management and Financial Planning in Supply Chain is cost optimization. With rising transportation costs, fluctuating fuel prices, and increasing labor costs, optimizing costs in the supply chain is no longer a luxury—it’s a necessity. Several strategies can help achieve cost optimization: Cost optimization in the supply chain not only ensures better profitability but also helps companies maintain competitive pricing in a rapidly changing market. Conclusion: A Unified Approach to Supply Chain Success Incorporating both logistics management and financial planning in supply chain offers businesses a holistic approach to maximizing supply chain performance. From warehouse and inventory management to cost optimization in supply chain, effective strategies across these areas can reduce inefficiencies, mitigate risks, and improve profitability. With the right blend of logistics expertise and financial foresight, companies can create more resilient, cost-effective supply chains that can weather disruptions and capitalize on new opportunities. By embracing Supply Chain Finance Solutions and applying robust Risk Management in Logistics, businesses can stay ahead in today’s fast-paced, competitive landscape. This approach will ensure that your supply chain not only runs smoothly but also remains profitable, adaptable, and sustainable in the long run. For expert solutions in logistics and financial planning, contact Aventex Consulting—your trusted partner in efficient supply chain management.